О ситуации с чипами в России: «90% компаний не могут с нами работать»
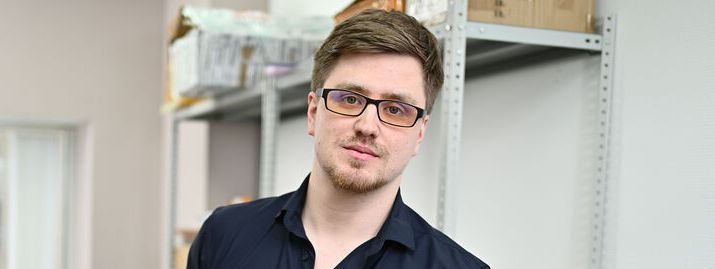
Из-за санкций произошла кардинальная перестройка всей структуры производства электронных компонентов в России, считает глава отечественной компании по сборке микросхем «Элодика» Константин Кириллов. В интервью «Газете.Ru» он рассказал, как в условиях многомесячных санкций продолжает работать индустрия, сможет ли Россия догнать Тайвань с его инновациями или только «дружественный Китай» поможет ликвидировать отставание от лидеров. В развитие темы ВиД публикует колонку имеющего зарубежный опыт в отрасли Дениса Шамиряна.
Кардинальная перестройка
— В каких отраслях российской экономики компоненты для микроэлектроники наиболее востребованы?
— В России без них не обходятся системы связи, освещение, вентиляция, блоки управления и т.д. Они есть в любом современном приборе: пылесосе, компьютере, холодильнике, домофоне, умной колонке.
Российские производители используют в своих изделиях как отечественные, так и импортные компоненты, но импортных намного больше.
Львиную долю выручки приносят микросхемы и транзисторы.
— Как в настоящее время себя чувствует российский рынок компонентов?
— Он переживает непростые времена. Раньше мы были дистрибьюторами тех или иных зарубежных компаний, имели с ними какие-то дилерские отношения.
Рынок быстро приспосабливается к новым вызовам и ситуации в целом, хотя в последние полгода произошла кардинальная перестройка всей его структуры.
Сейчас Россия находится под санкциями, что блокирует работу с «привычными» импортными компонентами.
close00— Решает ли эту проблему параллельный импорт?
— Да, для многих предприятий это теперь основной канал поставок электронных компонентов. Параллельный импорт дает возможность соблюдать сроки производства и сохранить привычную стоимость конечного продукта. А главное — он может обеспечить производителей необходимыми компонентами «здесь и сейчас».
90% зарубежных производителей не могут работать с Россией из-за санкций. Все, что нам остается, — это Азия и параллельный импорт.
У мировых производителей и дистрибьюторов заполненные склады. И параллельный импорт в Россию для них тоже выгоден. Главное, чтобы «никто об этом не знал».
Соперничество в чипах
— Могут ли российские производители составить серьезную конкуренцию иностранным поставщикам?
— Вопреки сложившимся стереотипам, российские предприятия выпускают хорошую качественную продукцию. Не поверите, многие такие изделия даже спустя 20 лет работают хорошо.
На складах до сих пор лежит отечественная продукция 90-х годов, и люди покупают ее! Они знают, что эти компоненты будут функционировать.
Во многих изделиях за 30 лет технология практически не изменилась. Может, поменялся корпус, но «начинка» сохраняется прежней.
— Но почему тогда за рубежом предпочитают не российские чипы?
— Минусы «наших» изделий — маленький ассортимент, отсутствие гибкости, сроки и объемы производства. Например, завод выпускает пять линеек микросхем.
Они качественные, но у импортных компаний этого же сектора может быть 50 таких линеек. Поэтому львиная доля российских потребителей этой продукции все равно будет рассматривать импорт.
Ни у одного нашего завода нет большого складского запаса. Поэтому многие предприятия отказываются от наших поставщиков в пользу импортных.
Клиентам приходится долго ждать продукцию или заказывать сильно заранее. На некоторые позиции очередь больше года.
Еще один вопрос — в цене. Некоторые детали дороже импортных, иногда намного. Хотя по качеству они не уступают Китаю и Тайваню, а иногда даже превосходят их.
— А сколько стоит российская деталь по сравнению с импортной и почему такая разница в цене?
— Например, чип резистор RC0805FR-07100RL. В импорте его цена от 16 копеек, а русский аналог Р1-12 ШКАБ.434110.002 начинается от 10 руб. Или DC-DC преобразователи (применяются для изменения выходного напряжения электричества. — «Газета.Ru»). Импортный MAX1644EAE можно встретить от 400 руб., а отечественный 1310ПН1У сейчас продается от 600 р.
И все виды чипов резисторов, кондесаторов — импортная замена тоже в разы дешевле отечественных аналогов. Такая разница в цене обусловлена масштабами продаж и стоимостью производства.
Глобализация рынка компонентов
— Учитывая все минусы, смогут ли отечественные производители обеспечить все потребности внутри России?
— Самообеспечение на этом рынке — очень сомнительная цель. Микроэлектроника развивается стремительными темпами. По всему миру происходят научные открытия, появляются новые разработки, тенденции и изобретения.
Разные страны на этом рынке дополняют друг друга. Да и в целом современная международная экономика — это не про «замещение», а про сотрудничество.
Правильнее говорить о соответствии продукции современным требованиям рынка. Поставщики и производители должны быстро реагировать на мировых лидеров в этой сфере и добавлять новые линейки продукции.
Военная промышленность и умные колонки
— Как сильно изменилась деятельность «Элодики» в условиях многомесячных санкций?
— К основным сложностям нынешнего времени можно отнести постоянно меняющиеся условия работы. Правда, мы все равно пока не планируем выходить за рубеж. У нас большие планы на российский рынок.
Среди наших клиентов можно отметить «Яндекс», «Ростех», «Роскосмос», «Вертолеты России», концерн «Созвездие» и «Росэлектронику».
«Яндекс» закупает у нас комплектующие и заказывает монтаж печатных плат. «Яндекс.Станции» работают именно на них. Сейчас «Яндекс» дорабатывает своих роботов-доставщиков, и мы тоже принимаем в этом участие.
Мы начинали в 2017 году с девяти клиентов, а теперь примерно 90% наших заказчиков — государственные и окологосударственные проекты развития и модернизации страны.
— Как изменился спрос на вашу продукцию в 2022 году?
— В 2022 году у государства сместились приоритеты в сторону оборонной промышленности. В некоторых случаях облегчился порядок взаимодействия с заказчиками, упростились бюрократические процедуры. Скорость, гибкость и нацеленность на результат стали последними тенденциями рынка.
— Была история про то, что российские военные вынимали чипы из стиральных машин, чтобы их вставлять в военную технику. Интересует ваше мнение как специалиста, насколько это реалистично?
— Забавная история. Теоретически, конечно, возможно все. Можно и сову на глобус попытаться натянуть, только зачем? Все электронные компоненты имеют взаимозаменяемые аналоги, их огромное множество.
Извлекать условный контроллер из бытовой техники для его дальнейшего использования в военных целях — очень трудоемко и иррационально, его проще купить.
Если же такая странная история была, надо отдать должное гибкости мышления и изобретательности исполнителя.
— Как вы поставляете иностранные компоненты для собственного производства в условиях санкций?
— У нас налаженная за пять лет логистика, за счет чего нам в рамках параллельного импорта гораздо легче, чем другим игрокам. И все равно признаюсь, что имеются определенные трудности.
На самом деле параллельный импорт был всегда. Просто официальным дилерам больше доверяли: «Это надежно, мы лучше немного переплатим».
Но с весны этого года все стало еще интереснее. Под санкции попали микросхемы, чипы и так далее. Предприятия, которые все это производят, не могут привезти комплектующие. Сейчас сохраняются небольшие официальные поставки китайских производителей, и на этом, по сути, все.
— Какие компании, производящие чипы, ушли с российского рынка?
— Такие компании как Schneider Electric, NXP и Analog Devices, приостановили работу с Россией, их продукция используется в огромном множестве изделий, но это не говорит о том, что аналогов им нет.
Догнать Тайвань?
— Может ли Россия самостоятельно справиться с проблемой нехватки чипов? Догнать Тайвань?
— Производства микроэлектроники в Китае, США, Южной Корее и Тайване имеют большой инвестиционный и исторический бэкграунд. В этих странах мощные производственные и технологические базы, много специалистов и привлекательные условия для развития на мировом уровне.
Может, это звучит слишком самоуверенно, но Россия вполне может догнать мировых лидеров. Для этого нужно в первую очередь создать благоприятную бизнес-среду. Не будет лишней и финансовая поддержка отрасли государством. Будущее у российской микроэлектроники есть, мы его строим и приближаем.
— Сколько нужно времени и ресурсов, чтобы выйти на мировой уровень?
— Еще раз повторю — все далеко не так плохо, как принято считать. Заводы готовы масштабироваться, наращивать производственные мощности, более оперативно выпускать продукцию, снижать цену.
Но все упирается в то, что люди «здесь и сейчас» все равно покупают импорт. Насколько для наших заводов актуально рисковать и закупать станки за десятки миллионов долларов?
Лично я бы не рискнул: слишком неоднозначная ситуация. Непонятно, что будет дальше, в какую сторону повернет рынок.
— Чего ожидаете от своей индустрии в ближайшие пять лет?
— В ближайшие пять лет я не ожидаю роста производства отечественных компонентов: нет гарантии сбыта. Допустим, все санкции сохранятся еще несколько лет.
При этом дружественный нам Китай быстро построит заводы и закроет все потребности России в этой сфере.
Здесь может помочь законодательство. Например, установить квоту для импортных комплектующих — условно говоря, не более 30%. Тогда наши производители увидят перспективу и начнут развиваться.
— Не видите опасности в такой большой роли Китая в вопросах поставок технологий? Ведь один из лидеров вряд ли захочет отдавать целиком свое преимущество, пусть и за большие деньги.
— Мы не видим в этом опасности. Китай, как и другие страны, с кем мы ведем торговлю, дает выгодное предложение по стоимости и ассортименту продукции микроэлектроники, но это не говорит о «зависимости» от них, скорее о большей привлекательности продукции, только и всего.
Ряд компаний действительно выставляют условия на использование выпускаемой микроэлектроники, например на предприятиях военно-промышленного комплекса, но всегда есть аналоги.
Валерий Романов.
На снимке: Константин Кириллов.
Попытка обобщения
Микроэлектроника в России до и после 24.02.2022
В качестве уточнений и обобщений ВиД предлагает прочитать колонку Дениса Шамиряна на ресурсе «Хабр», в которой автор, имеющий более чем 20-летний опыт работы в отрасли, в том числе 15 лет за границей, как в R&D (IMEC), так и на массовом производстве (Global Foundries), постарался ответить на вопросы в каком сейчас состоянии российское микроэлектронное производство и сможет ли Россия создать полностью локальное производство чипов.
Сразу оговорюсь, что данная статья не претендует на всесторонний независимый анализ ситуации, а отражает мою личную точку зрения, основанную во многом не на открытых источниках, а на опыте: личном общении, мнении других специалистов; в общем всём том, доказательств чему найти нельзя или очень сложно. Поэтому пруфов предоставлять не буду – каждый имеет собственную точку зрения и право ее высказывать (по крайней мере пока).
Говорить я буду только про технологии производства, так как сам я бывший технолог, к дизайну отношения никогда не имел и фразы типа «лицензирование ядер процессора» для меня темны и непонятны.
Также отмечу, что говорить буду только про КМОП производство, во-первых потому, что эта тема наиболее интересна потребителям (это бытовая электроника – процессоры, память и т.п.), во-вторых, за границей я работал в КМОП (aka CMOS) производстве и хорошо представляю его изнутри, в-третьих сам я сейчас работаю в МЭМС индустрии и писать про нее не буду, так как являюсь заинтересованной стороной.
Статья состоит из трех частей:
- Анализ текущих производителей
- Размышления на тему полностью локального производства микроэлектроники
- Попытка заглянуть в будущее
Анализ текущей ситуации
Для начала давайте посмотрим на текущих производителей микроэлектроники. Я буду говорить только о более-менее современных фабриках, способных выпускать микросхемы по техпроцессу 180 нм и ниже. Чтобы было понятно, я буду приводить примеры процессоров, произведенных по определенной технологии, данные взяты из Википедии там в статье есть справа колоночка со всеми техпроцессами, можно кликнуть и посмотреть, что по этому техпроцессу (и когда) производилось. Так вот, 180 нм – это начало 2000-x, процессоры типа Intel Celeron и PlayStation 2. Всякие старые советские заводы (типа НЗПП), работающие по технологиям больше микрона, рассматривать не будем (например, Intel 80286 был сделан по технологии 1.5 мкм).
Небольшая оговорка про размер пластин. Современное производство работает либо на 200 мм (до 90 нм), либо на 300 мм (65 нм и ниже) кремниевых пластинах. Наиболее продвинутое оборудование для технологий меньше 65 нм существует только в варианте 300 мм. Поэтому сделать высокие технологии на 200 мм пластинах не получится. А оборудование для 300 мм пластин существенно (в разы) дороже оборудования для 200 мм пластин.
Итак, что мы имеем на сегодняшний момент.
Микрон
Микрон - это наиболее живое микроэлектронное производство в России. Работают на 200 мм пластинах, обладают технологией 180 нм (в массовом производстве), 90 нм (не уверен, что в сильно массовом, но могу ошибаться; 90 нм – это Intel Celeron M/D, AMD Athlon 64), 65 нм (тут у меня большие сомнения что там есть массовое производство; 65 нм - это AMD Turion 64 X2, Microsoft Xbox 360 "Falcon"). Я в свое время участвовал в попытках разработки технологии 65 нм на 200 мм пластинах (IMEC, Бельгия), но оборудование не тянуло, поэтому 65 нм техпроцесс был перенесен на 300 мм оборудование.
Производит Микрон в больших объемах в основном чипы для банковских карт, паспортов, билетов в метро и т.д. В небольших объемах производят то, за что попали под санкции. Находятся под санкциями довольно давно, так что уже как-то научились с этим справляться. Оборот более 6 млрд рублей, из них примерно половину они зарабатывают сами, остальное докидывает государство (например, в виде субсидий по 109 постановлению Минпромторга – Микрон там всегда среди получателей субсидий).
Ангстрем-Т
Не путайте с просто Ангстремом (без Т) – Ангстрем это как раз старое советское производство, они делали чипы для советских калькуляторов и игры «Ну погоди» - если кто настолько стар, чтобы ее помнить, там волк яйца из-под куриц ловил. Ангстрем до сих пор жив и производит продукцию (понятное дело, не для калькуляторов).
История Ангстрема-Т началась в 2007 году, когда Global Foundries (тогда это был еще завод AMD – Fab36, Дрезден), начал переход на 300 мм пластины и продал все оборудование и технологии на 200 мм Ангстрему-Т: 130 нм (уровень AMD Athlon MP Thoroughbred) полная документация на техпроцесс с гарантией выхода годных и 90 нм – разработана, но еще не в массовом производстве. На тот момент это были довольно свежие технологии. Но дальше что-то пошло не так. Оборудование застряло на складе в Роттердаме, и когда я пришел работать на Global Foundries в 2011 году, это было уже притчей во языцех – как они продали оборудование в российскую компанию, но оно, вместо того, чтобы использоваться, уже 4 года гниет на складе. Гнило оно еще где-то до 2014, после чего все-таки приехало в Россию. В Зеленограде был построен завод, практически точная копия дрезденского, они даже построили собственную электростанцию, чтобы покупать не электричество, а газ и вырабатывать электроэнергию своими силами, чтобы не зависеть от перебоев с электроэнергией. Так же сделано в Дрездене, правда, немцы ухитрились сами себе отключить электричество на заводе (как раз в мое дежурство) – но это уже другая история.
Так вот, завод был построен, оборудование завезено, я там был и испытывал дежавю после Дрездена – все точно так же, установки на тех же местах, с теми же кодовыми названиями.
То есть, выглядело там все более-менее нормально, но вот с руководством там какая-то странная история. У меня есть целая коллекция визиток генеральных директоров Ангстрема –Т одинакового дизайна, только фамилии разные – они там менялись постоянно (вместе со всей командой). Как-то раз общался с одним из замов, он меня спросил, как у нас устроен контроль качества, я рассказал, он начал смеяться и сказал, что я ничего не понимаю в контроле качества. Ну, у нас контроль качества устроен по тем же принципам, по которым я в Германии делал чипы модемов для Qualcomm для пятых айфонов, Эппл вроде на качество не жаловался. Так что я пожал плечами, но спорить не стал. Еще как-то раз я беседовал с VP sales ASML, он интересовался, как там дела у Ангстрема-Т и сказал, что так как их сканеры простояли 7 лет на складе, запустить их будет очень сложно и предложил сдать старые сканеры в трейд-ин, а в Ангстрем-Т поставить более новые с доплатой. Я пересказал этот разговор руководству Ангстрема-Т и сказал, что по моему мнению это неплохая опция – они получат быстрый результат лучшего качества, пусть и за дополнительные деньги. Руководство Ангстрема-Т сказало, что оно ничего про это предложение не знает. Странно, подумал я, какой-то левый чувак вроде меня знает, а те, кому это предлагали и для кого это должно быть важно – нет.
Итог – с момента покупки линии прошло уже 15 лет, производство до сих пор не работает. Заработает ли когда-нибудь, мне не ведомо. На данный момент предприятие обанкротилось.
Крокус наноэлектроника
Исходная идея Крокуса – это производство MRAM – магниторезистивной памяти. Не буду углубляться в детали, вкратце – вы получаете энергонезависимую память (как на флешках) которая работает со скоростью оперативки (как DRAM). От этого сочетания слюнки текут у многих, поэтому многие пытались ее сделать (я точно знаю про Sony и Infineon). Проблема оказалось в том, что теоретически все красиво, но в реальности получилось не очень, точнее, получилось, но вот быстродействие оказалось на уровне обычной флеш-памяти, а флеш-память уже есть, зачем городить еще одну технологию для того, что уже прекрасно работает?
Но, до того, как это стало ясно, Роснано решило проинвестировать в фабрику 300 мм по техпроцессу 65 нм на территории России. Вы можете как угодно иронизировать над Роснано, но на данный момент это единственная в России фабрика на 300 мм пластинах с работающей технологией 65 нм. Правда, есть нюанс.
В исходной модели предполагалось, что MRAM ячейки будут изготавливаться на уровнях металлизации (так называемый back end). Так как сами транзисторы (front end) можно изготовить на любой фабрике, это легко доступный товар, было решено не тратиться на фабрику полного цикла, а построить часть фабрики, которая будет содержать только know-how по изготовлению MRAM. Замечу, кстати, что оборудование для front end стоит гораздо дороже (его там просто больше всякого разного, а для back end много, в принципе, не нужно). Так что исходная модель выглядела так:
- Строим полу-фабрику (только back-end) за разумные деньги
- Покупаем пластины c front end за небольшие деньги на мировом рынке
- Добавляем MRAM back-end
- Продаём за большие деньги на мировом рынке
- PROFIT!
Если бы MRAM технология заработала, это было бы очень красивое решение. Но она не заработала (причем не только у Крокуса), и Крокус превратился в эдакий чемодан без ручки.
С одной стороны, он не является полноценной фабрикой, так как не делает транзисторы (front end), а заказывать на иностранной фабрике front end а потом доделывать у себя бессмысленно, проще сразу заказать на иностранной фабрике полный цикл. Если же тебе откажут в полном цикле, то откажут и в половине цикла.
С другой стороны, это единственное в России работающее производство на 300 мм пластинах по 65 нм техпроцессу, с возможностью дальнейшей модернизации до 45 нм и, может быть, до 32 нм.
То есть, и убить жалко, и что дальше делать – непонятно. Достроить до полной фабрики? Но это огромные инвестиции, да и место там физически не особо есть под полную фабрику. То есть, надо переносить. А если переносить – не проще ли с нуля тогда построить? (обычно проще). А обанкротить – рука не поднимается.
Годовой оборот Крокуса – это где-то миллиард рублей, сами они зарабатывали процентов десять (в основном разовые заказы на напыление магнитных материалов для иностранных заказчиков – российских нет, так как в России нет 300 мм фабрик).
Новый завод в Зеленограде
Про него мало что известно. Размер пластин 300 мм, техпроцесс 65 нм – 45 нм (First generation Intel Core i3, i5 and i7). Строить его планировали уже давно, вот например, новость (неизвестной датировки), что к 2014 году должны построить. Строить собиралась компания Ситроникс, но ничего внятного нагуглить не удается. Несколько лет назад мне из правительства присылали на экспертизу техзадание на завод, я почитал – написано было грамотно, явно писали люди, которые знали, что они делали. По слухам, строительство идет, с привлечением китайских подрядчиков (вроде как UMC - правда, это Тайвань). Больше ничего сказать не могу. Что из этого получится, тоже не понятно.
Итог
На Микроне теоретически можно производить что-то уровня Intel Celeron/AMD Athlon 64 (техпроцесс 90 нм, середина 2000-х). Чтобы двигаться дальше, нужен завод на 300 мм, а его в полностью функциональном состоянии нет.
Можно ли полностью локализовать производство микроэлектроники по современному техпроцессу?
Короткий ответ: нет.
Более подробный ответ: Ни одна страна в мире не сможет локализовать производство микроэлектроники по техпроцессу меньше 90 нм. Наладить что-то вроде микронной технологии (контактная литография, жидкостное травление, ручные операции) на коленке еще как-то можно, но это будет уровень 8086/80286 или ZX Spectrum.
Развернутый ответ. Для успешного микроэлектронного производства необходимы следующие факторы:
- Наличие рынка сбыта
- Наличие производственного оборудования
- Наличие компетентного персонала
- Наличие сырья, материалов и расходников
Давайте разберем каждый аспект подробнее.
Рынки сбыта
Казалось бы, какие рынки сбыта – если надо сделать, значит надо, не считаясь с затратами. Проблема в том, что сам полупроводниковый завод – это только верхушка айсберга. И не считаясь с затратами придется пилить весь айсберг, а это очень и очень много денег.
Все привыкли к тому, что полупроводниковые чипы очень дёшевы. Почему они получаются дешевыми, я писал в другой статье. Многие ошибочно полагают, что достаточно поставить завод на территории России и мы получим такие же дешевые чипы, только произведенные дома. К сожалению, это не так. Полупроводниковый завод сжирает огромное количество денег, независимо от того, производит он что-то или нет. То есть, чтобы один чип был дешевым, нужно это огромное количество денег разделить на огромное количество чипов (десятки миллионов для завода средней руки). А их надо куда-то сбывать. Если сбыть их некуда (российский рынок не такой большой), то завод будет нести убытки, которые либо должно покрыть государство субсидиями (тогда чипы будут дешевыми для потребителя), либо сами потребители (тогда чипы будут очень дорогими). То есть, если вы хотите делать по настоящему дешевые чипы, вам нужно их продавать всему миру.
Следующий слой айсберга – это оборудование. Заводу нужно примерно десяток установок одного типа (например, литографии, или травления), а типов таких десятки (если не сотни). Производителю оборудования одного типа не интересен рынок из десяти штук – опять, либо оборудование будет золотым для завода, либо производителя оборудования должно субсидировать государство. Либо фабрик должно быть много, тогда у производителя оборудования появляется рынок сбыта и его продукция дешевеет. Но много фабрик нам не нужно – мы с одной то не знаем, куда чипы девать. То есть, если вы хотите сделать относительно недорогое оборудование (относительно недорогое – это значит что, например, установка фотолитографии стоит примерно как Боинг), его нужно продавать по всему миру.
Следующий слой айсберга – комплектующие для оборудования – электроника, насосы, роботы и т.д. Тут та же история – для десятков/сотен единиц оборудования много насосов не нужно, и мы опять утыкаемся либо в высокую стоимость, либо в необходимость продавать на мировом рынке.
И такая же история будет со всем остальным: с кремниевыми пластинами, химикатами, системой водоподготовки. Все, что будет уникальным для нашего производства, будет дико дорогим, так как больше мы это никому не продадим (ну либо мы торгуем со всем миром).
Еще один момент. Один завод не может производить всю микроэлектронную номенклатуру. То есть и процессоры, и оперативную память, и флеш-память, и микроконтроллеры и радиомодемы и т.д. и т.п. в один завод не втиснуть. Производство оперативной памяти – это вообще отдельная отрасль микроэлектроники с отдельными заводами, техпроцессами и игроками. В свое время немцы пытались сыграть в эту игру, Infineon отпочковал компанию Qimonda, которая должна была заняться производством оперативной памяти. Не получилось. Себестоимость чипа памяти, произведенной на Qimonda была равна стоимости чипа памяти Samsung на прилавке в магазине. Qimonda обанкротилась.
То есть, чтобы иметь полностью локализованное производство, нужно иметь несколько заводов. И куда-то продавать продукцию этих заводов. Либо содержать эти заводы, работающие с минимальной загрузкой. Справедливости ради отмечу, что много заводов создадут хоть какой-то спрос на оборудование и сырье.
Давайте примерно прикинем, сколько это стоит. Для примера, Интел строит новый завод в Германии за 17 млрд долларов. Нужно несколько заводов, допустим это будет $50-60 млрд. Для сравнения, это расходы на оборону в России в 2020 г. Вся экосистема, я думаю, будет стоить как минимум на порядок больше, то есть $500-600 млрд. Это уже треть ВВП России. А ведь такая экосистема может обойтись и дороже, чем на порядок.
В итоге, создать и содержать полностью локализованное производство – это ОЧЕНЬ дорого.
Производственное оборудование
Допустим, мы где-то нашли квадрилиарды денег и можем себе позволить все. Первое что нужно – это оборудование. Замечу, что на данный момент нет ни одной страны в мире, которая производила бы все оборудование, необходимое для микроэлектронного производства по технологиям 45 нм и ниже. Даже США, которые производят львиную долю полупроводникового оборудования, не производят машины фотолитографии. Их производят либо Нидерланды (ASML), либо Япония (Nikon, Canon). Applied Materials (США), один из крупнейших (а может и крупнейший) производитель оборудования, обычно хвастается, что может поставить полную линейку оборудования только из своих машин, но всегда добавляет: кроме фотолитографии.
Сделать оборудование для современного полупроводникового производства очень трудно, а самому с нуля – невозможно. Тут есть два момента.
Во-первых, современные производители оборудования прошли огромный путь в десятки лет улучшая и совершенствуя свое оборудование. Для примера, голландский производитель фотолитографического оборудования, компания ASML потратила около 15 лет, чтобы довести до ума установку EUV. Первый прототип был поставлен в IMEC (где я тогда работал) в начале двухтысячных, а на рынок она вышла несколько лет назад (это я еще не знаю, сколько времени у них заняло первый прототип сделать). Это при том, что у ASML огромный опыт в разработке и производстве машин фотолитографии и их R&D бюджет составляет порядка миллиарда евро в год (я думаю, львиная доля этого бюджета уходила и уходит на EUV).
Во-вторых, современное оборудование – это фактически конструктор лего, в котором 90% блоков стандартных (роботы, вакуумные насосы, котроллеры газовых потоков и т.д. и т.п.) и 10% - это ноу-хау компании, на которое и тратится основное время и деньги при разработке. Насколько мне известно, компоненты полупроводникового оборудования необходимого качества в России не производятся.
Можно, конечно, попробовать все сделать самому – но это как раз одна из причин, почему прогорела наша родительская компания Mapper Lithography: они все пытались сделать сами: блоки питания, ВЧ генераторы, написать свой софт и т.д. В итоге машина работала час, потом ломалась и ее неделю чинили.
Также нужно не забыть, что помимо производственного оборудования необходимо вспомогательное: системы водоподготовки (и это не на кухне фильтр поставить), компрессоры для сжатого воздуха, генераторы азота и т.д. и т.п. Это все тоже нужно где-то брать, сейчас эта техника вся импортная.
Вывод: можно что-то попытаться сделать, если есть доступ к стандартным комплектующим высокого качества, если еще и комплектующие самому делать, то на мой взгляд, это невозможно. Плюс к этому то, что я писал в разделе про рынки сбыта, даже если сделать оборудование, то кому продавать, одному заводу? Но, хотя можно попытаться продавать в Китай – там фабрик много.
Компетентный персонал
Это видится наименьшей из проблем, но есть нюанс. В принципе, российские ВУЗы выпускают достаточное количество специалистов, которые после нескольких лет обучения вполне способны работать на современном производстве. Это подтверждается и опытом нашей компании и тем фактом, что многие специалисты российского происхождения работают на зарубежных полупроводниковых производствах (я и сам там работал, и многих русских знаю, кто работает).
Теперь про нюансы: во-первых, специалистов нужно обучить, доморощенные специалисты получаются плохо, особенно в области культуры производства и менеджмента качества. По моему опыту, качество – это головная боль российских компаний. Все могут наклепать аналоговнетов в единственном экземпляре, но вот поставлять продукцию устойчивого качества получается мало у кого. При наличии руководства/ведущих инженеров имеющих зарубежный опыт работы поставить менеджмент качества не составляет большого труда, но у чисто российских компаний это получается плохо. Помните, как я писал выше что производственное руководство Ангстрем-Т посмеялось над нашей системой менеджмента качества? Вот это как раз про то. В общем, иностранные (либо экспаты, либо россияне с зарубежным опытом, вроде меня) специалисты могут приехать и научить, вопрос, как их теперь заманить?
Второй нюанс: как только инженеры-технологи становятся более-менее опытными специалистами (несколько лет опыта на нормальном производстве), они тут же начинают смотреть за рубеж. Инженер-технолог на полупроводниковом производстве в Европе получает 3-4 тыс евро на руки (для понимания уровня расходов приведу в пример Дрезден: съем 3-комнатной квартиры 700-800 евро, питание 200-250 евро на человека, одежда раза в полтора дешевле, чем в Москве). В итоге происходит постоянная утечка кадров, так как за рубежом инженеры-технологи нужны всегда (хоть и не так остро, как IT специалисты), а платить как за рубежом мы, к сожалению, себе позволить не можем.
В итоге, для нашего гипотетического завода мы должны пригласить иностранных специалистов с их технологиями управления, а потом удержать своих специалистов от эмиграции.
Сырьё и материалы
Для работы завода нам понадобятся кремниевые пластины, жидкая химия (особенно фоторезист), газы, всякая мелочевка (типа перчаток, масок, пинцетов и т.д.). Причем все это не абы какого качества, а очень высокой степени очистки, мелочевка совместимая с чистыми помещениями и т.д. Со всем этим ситуация в России не то, чтобы очень радужная. Интересный пример с масками. Когда начался ковид, наш поставщик масок (специальных для чистых комнат, обычные медицинские там не подходят) сказал, что они все мощности бросили на медицинские маски и специальных теперь не будет. Пришлось изобретать многоразовые и стирать. В России такие маски не производят.
Пытались работать с отечественным фоторезистом. То пузыри, то мусор, то к пластине не липнет. Каждая партия отличается от предыдущей, приходилось каждый раз подстраивать параметры процесса для новой партии. Приходил в негодность за два месяца до срока годности (иногда, а иногда даже после истечения срока годности был нормальный). В общем, поиграли в рулетку где-то годик, перешли на американский. Настроили процесс один раз и забыли про проблемы. И это был фоторезист на микронные размеры. Как обстоят дела с российским фоторезистом на технологии менее 65 нм – я не знаю.
Кремниевые пластины. Есть прекрасная российская компания, которая их производит. Номенклатура не очень большая, но самые ходовые размеры есть. Качество хорошее. Но, как обычно, есть нюанс. Пластины нарезаются из импортных кремниевых слитков, на импортном оборудовании с использованием импортных расходников (запас которых, как нам сообщили на два месяца, новых поставок пока нет). То есть, если мы хотим полностью локализованное производство нам нужно наладить еще производство слитков (для этого тоже нужно оборудование разработать и произвести), производство машин для резки, шлифовки и полировки и расходников к ним.
Фотошаблоны. В России есть производство фотошаблонов на более старые технологии (точно не на 45 нм и ниже), ну и, естественно, на импортных стеклах и импортном оборудовании. Производство современных фотошаблонов – это тоже целая индустрия, производителей в мире не так много (один из примеров компания AMTC в Дрездене). Там тоже нужно оборудование, сырье и материалы и т.д. и т.п.
Выводы
Нельзя просто взять и построить завод по производству микроэлектроники. Для такого завода нужна огромная экосистема (потребители (много потребителей), оборудование, сырье и материалы, кадры). Недавно была переводная статья про такую экосистему Причем экосистема эта очень хрупкая, при исчезновении хотя бы одного компонента вся система рушится. Создать такую экосистему полностью изолированную от внешнего мира на мой взгляд, невозможно.
И что дальше?
Короткий ответ: я не знаю.
Как это могло бы выглядеть? При интеграции в мировую микроэлектронную экосистему (имея возможность покупать оборудование, сырье и материалы и возможность продавать продукцию) выбрать нишу, в которой нет жесточайшей конкуренции (как в производстве памяти и процессоров) и пытаться занять там свою долю играя на более низкой стоимости труда и уникальных системных решениях толковых местных инженеров. Например, в области ВЧ микроэлектроники. Насколько я знаю, в уже упоминавшемся Ангстреме-Т есть (были?) неплохие наработки по таким направлениям, а они могли бы быть востребованы в IoT, который растет довольно быстрыми темпами. Ну или какую-нибудь силовую интегральную электронику. Или интегральную фотонику. Имея пару высокотехнологичных заводов, встроенных в мировую экосистему, можно уже и какие-то вещи делать, которые не хочется, чтобы другие видели.
За железным занавесом (имеется в виду полная локализация от начала до конца) можно делать только что-то вроде 80286 процессоров за огромные деньги, не более того. Я думаю, глобализация потому и происходит, что в одиночку выше определенного технологического предела продвинуться невозможно – ни одна страна не потянет, только всем миром. Будем ли мы частью этого мира – это отдельный вопрос.